Créée en 2017 pour valoriser 30 ans de recherche menées au SIMaP, Vulkam entend rien moins que révolutionner la métallurgie grâce au développement de métaux amorphes. La start-up a en effet breveté plusieurs alliages métalliques dont l’organisation atomique a été modifiée. Tandis que dans un alliage métallique classique (cristallin), les atomes sont organisés de façon ordonnée, dans les métaux amorphes, également appelés « verres métalliques », ils se présentent de façon aléatoire. Cette structure désorganisée offre des propriétés inégalées en termes de dureté, de résistance à l’abrasion, comparables à celles des céramiques mais sans être fragiles.
Des avantages valorisables dans l’industrie
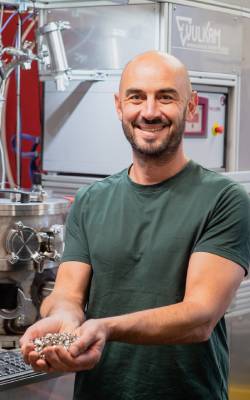
Ainsi, les alliages métalliques amorphes se distinguent par leur résistance trois fois supérieure à celle des métaux classiques, une flexibilité doublée, tout en étant plus légers. Ces qualités leur permettent de répondre aux enjeux des industriels et ouvre la voie à de nouvelles possibilités pour leurs petites pièces.
« Nous nous focalisons sur la miniaturisation, économiquement plus rentable, indique Sébastien Gravier, fondateur et PDG de Vulkam.
Nos produits permettent de miniaturiser les dispositifs médicaux, ou d’augmenter la durée de vie des systèmes mécaniques. Nous nous adressons d’ores et déjà aux industriels de l’horlogerie, du médical et de l’aérospatial, demandeurs de pièces métalliques en grands volumes et à haute valeur ajoutée. Mais d’ici à cinq ans, nous espérons innover avec de nouvelles compositions de matériaux pour d’autres segments de marchés, comme les transports mais aussi les sports et les loisirs. »
En outre, les procédés de production par thermomoulage développés et brevetés par Vulkam, permettent de réduire drastiquement les quantités de matières premières nécessaires. Cette technique, proche de l’injection plastique ou de la fonderie sous pression, permet la fabrication directe -sans opération supplémentaire d’usinage et donc de déchets - de pièces atteignant des niveaux de précision de quelques micromètres.
« On estime que les économies de matières premières et les économies de CO2 qui en découlent s’élèvent à respectivement 50% et 30% au minimum par rapport à l’équivalent classique. »
Les 34 millions d’euros levés auprès d’investisseurs, de banques, et sous formes d’aides et subventions de l’Etat, serviront notamment à financer la construction d’une usine de 3000 mètres carrés en Isère, et la mise en route d’une ligne de production, d’ici à 2025. Elle conservera une salle d’expérimentation au SIMaP, avec qui elle créera un laboratoire commun. Ses effectifs, de 30 salariés aujourd’hui (dont 70% d’ingénieurs, docteurs et techniciens), devraient passer à 50 personnes dans les trois années à venir.
*CNRS, UGA, Grenoble INP - UGA